TECH TALK
TECHNICAL INFORMATION AND INFORMATIVE HELP ARTICLES
Drum Pump Selection Guide
A guide to factors that should be assessed and considered when choosing the right drum pump for your needs.
Given the wide array of options of drum pumps available in the market, it is essential to meticulously assess which drum and barrel pumps are most appropriate for each specific application. This assessment is influenced by various factors. The extensive variety of drum and barrel pumps adds complexity to the selection process. These pumps are particularly well-suited for portable systems, rapid transfers, testing, and the handling of harsh chemicals, among other uses. Due to the multitude of potential applications, no single drum pump can serve as the optimal solution for every scenario.
Step 1. Ask the Correct Questions
Begin by posing a series of targeted questions regarding the specific application for which you need drum and barrel pumps. The responses to these inquiries will clarify your drum pump requirements and facilitate the selection process. Here are seven critical considerations:
Q1. What are the Required Head and Flow rates?
Depending on the size of your containers and the necessary pressure requirements, your application may demand higher flow rates or head pressure.
Examples of common scenarios, where it is essential to utilise a drum pump with a higher flow rate and greater delivery head to ensure efficiency and effectiveness are:
When emptying larger IBCs, totes, or tanks, or when transferring fluids to a second storey.
The maximum flow rate will determine how much and how fast you can transfer fluids from a container. If you have a larger container and need to transfer it fast; a greater flow rate is needed. The flow rate is usually represented as Litres Per Minute (LPM).
The Pipe Warehouse UK range of Drum Pumps have a maximum flow rate of 150 LPM, meaning that; dependant on motor settings, the drum pump is capable of delivering a flow rate of anything from 0 - 150 litres every minute. Therefore, as an example; 600 Litres will take at least 4 minutes to transfer when operating at maximum flow.
Q2. What are the Chemical Considerations for Pump Selection?
When selecting a drum or barrel pump, it is ESSENTIAL to identify the specific chemicals involved in the transfer process. Key questions to consider include:
- Will the fluid being transferred be flammable or combustible?
- What pump materials are compatible with the chemicals in use?
To ensure safe and efficient chemical transfers, it is crucial to choose a drum pump constructed from materials that can withstand the properties of the chemicals involved.
Important Note: Assess whether any of the chemicals are corrosive, toxic, or flammable/combustible. These hazardous substances necessitate specialised pump material and construction to ensure safe handling and transfer.
Q3. What is the Fluid Temperature?
Many drum and barrel pumps are designed with specific temperature limits for their pump tubes. These limits are influenced by the materials used in the pump's construction, as well as the design and length of the pump tubes. To ensure safe and efficient fluid transfers, it is essential to consider the maximum temperature of the fluids being pumped.
Maximum temperature ratings can vary significantly between pump models, so it is important to verify the specific pump's specifications with the manufacturer in relation to the chosen materials before making a selection.
MATERIAL | MAX. TEMP |
---|---|
POLYPROPYLENE (PP) | 79°C |
PVDF | 60°C |
STAINLESS STEEL 316 | 105°C |
Chart showing general range in which the material is considered suitable for most fluid transfer purposes. This chart is a guide only. Always check.
Q4. Do I Need to Consider the Specific Gravity and Viscosity of Fluids?
When selecting a pump for your application, it is essential to consider the specific gravity and viscosity of the fluid being handled. Fluids with high specific gravity or viscosity require specialized pumping solutions. While certain pump series and motors are designed to accommodate these characteristics, others may not possess the necessary capabilities, leading to suboptimal performance.
To ensure effective operation, it is critical to verify the specific gravity and viscosity ratings of the fluid. We recommend consulting the Safety Data Sheet (SDS) provided by the manufacturer for accurate specific gravity information. Additionally, please note that viscosity can fluctuate with temperature; therefore, it is important to use the viscosity value that corresponds to the temperature of the fluid being pumped.
Q5. What are the Container Size Considerations?
The size of the container plays a crucial role in selecting the appropriate drum pump model and determining the necessary pump tube length for your application. Intermediate Bulk Containers (IBCs), totes, and tanks require different pumping solutions compared to smaller containers and drums. When emptying or filling larger containers, it may be essential to utilise drum pumps capable of transferring larger volumes efficiently or that are equipped with extended tubes. Additionally, the size of the container can impact accessibility, further influencing your drum pump selection.
Refer to the chart below to assist in determining the correct pump tube length for your specific container size.
PUMP LENGTH | USUAL INDUSTRIAL APPLICATION |
---|---|
700mm | Usually used to transfer from 60 Litre Drums |
1000mm | Used to transfer from standard 200 Litre Barrels |
1200mm | Industrial Bulk Containers (IBCs) |
1500mm | Aiding transfers from process tanks |
1800mm | Aiding transfers from process tanks |
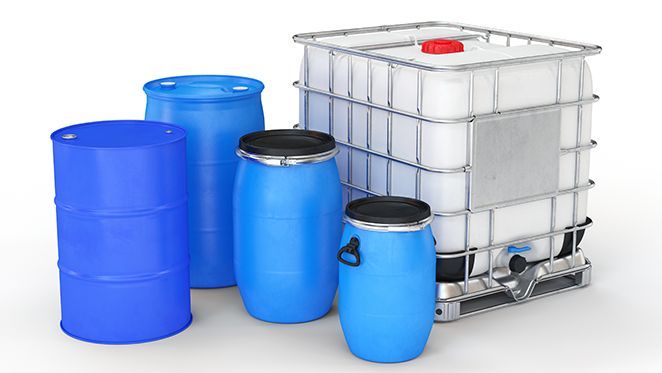
Q6. Do I Need to Consider Pump Size and Portability?
When selecting drum and barrel pumps, it is crucial to assess the importance of size and portability based on your operational needs. Certain environments may necessitate pumps that are easily transportable for various tasks throughout the facility, while others may require compact models that can fit into confined spaces.
If your application demands adherence to specific spatial constraints or requires high portability, these factors should be prioritised in your decision-making process. Additionally, if the pump will serve multiple functions, it is vital to ensure that its construction is safe and appropriate for each intended use, considering the other relevant parameters.
Be aware that drum and barrel pumps designed for handling highly viscous fluids tend to be larger and heavier, particularly those equipped with electric drive motors. To mitigate weight in such applications, consider opting for an air drive motor when feasible.
Q7. What are the Motor Selection Considerations for Drum Pumps?
When selecting a motor for drum and barrel pumps, it's important to consider the various options available. Common motor types include air, electric, and explosion-proof electric motors, with electric motors offered in different voltage configurations.
To determine the most suitable motor for your application, assess the specific environment in which the pump will be utilised.
Key Motor Considerations:
- Ensure compatibility with the electrical systems in the intended setting by selecting a motor that matches the required phase, voltage, and frequency.
- If opting for an air motor, verify that there is sufficient air pressure and volume to support its operation.
By carefully evaluating these factors, you can choose the most effective motor for your pumping needs.
Step 2. Select the Best Pump
Using the insights gained from the considerations outlined in Step 1, identify the most suitable pump for your specific application. Begin by assessing the required materials, then explore the pump series that provides the best options tailored to your needs.
Construction Materials
Drum and barrel pumps are available with tubes made from a variety of materials. Common options for outer tubes include 316 stainless steel, PVDF, polypropylene & CPVC. Each material possesses unique properties that may impact performance. By analysing the results from Step 1, technicians can ascertain which materials are most appropriate for a given application.
It is also crucial to consider the construction of the entire pump assembly. The fluids being transferred will interact with more than just the outer tube. Furthermore, the external environment in which the pump operates can significantly influence the choice of exterior materials and the overall design of the pump.
A helpful resource for selecting materials is a chemical resistance guide. These guides are offered as an online resource to aid in the selection of tube and other wetted materials.
Pump Series Overview
Certain series from drum pump manufacturers are specifically engineered for a variety of applications. Some models excel in transferring large volumes of fluids quickly, while others are optimised for handling smaller quantities. It's important to note that not all series accommodate the pumping of flammable or combustible materials. Conversely, some are specifically designed for viscous fluids and include food grade options, making them suitable for the food and beverage industry.
Utilise the information gathered in the initial assessment to evaluate the drum pump series available from manufacturers or local distributors. This will help you identify the series and model that best align with your application requirements.
This is also an ideal time to determine the necessary pump tube length for your specific application.
Check Chemical Resistances of Pump Materials Below
OVERVIEW OF SPECIFICATIONS OF OUR PUMP RANGE
Transfers Viscous Solutions Rated up to 1500cps
Flow Rate up to 150 LPM
For solutions with Specific Gravity up to 1.8 SG
Discharge Head up to 1.2 Bar Pressure
Engineered for Medium to Heavy Industry Use
3. Choose the Right Motor
Drum pump motors are not all universally interchangeable. Each series of drum pumps may be designed to work with specific motors to ensure optimal performance. Many of these drum pump motors include speed control features, allowing for precise flow adjustments. Additionally, certain motor types are more suitable for specific applications. Below are the most common drum pump motor options along with their key features.
Splash-proof / Open Drip Proof (ODP) motors (IP24)
These high-speed motors are available in 110 and 240-volt, single phase and 50/60 Hz options. These drum pump motors are drip-proof and are protected in every direction from water splashes.
Our variable speed ODP Motors are all
825 Watts and available in either:
240v or
110v
Enclosed/TEFC Motors (IP54/55)
Enclosed motors are designed to provide superior protection against water splashes, dust, and corrosive fumes. Available in both high-speed brush types and slower-speed induction models, these drum pump motors are ideal for applications involving fuming chemicals and dusty environments. They represent a reliable solution for maintaining performance and durability in challenging conditions.
Pipe Warehouse UK do offer Enclosed Motors.
Contact us for details
Explosion-proof motors (IP54/55)
Similar to enclosed motors, this design is sealed to protect against corrosive fumes, water splashes, and dust. Additionally, these drum pump motors are specifically engineered for use in hazardous environments and are compatible with flammable or combustible liquids.
Pipe Warehouse UK do offer Atex Zoned Compliant Motors.
Contact us for details
Air motors
This motor design is lightweight and equipped with variable speed capabilities. Its non-electrical operation minimizes the risk of igniting flammable gases, enhancing safety in various applications.
See our Air Driven Drum Pump Motor
Lithium-Ion battery motors (IP24)
Unmatched in terms of portability and convenience due to the cordless design. They enable seamless fluid transfer anywhere you need it. There's no requirement for electric outlets or air connections. Typically found on medium performance pump series.
4. Choice of Accessories
Drum and barrel pumps can be accessorised with a variety of products to improve convenience, safety, and effectiveness for various applications. When selecting a drum pump, consider the following common accessories and how they might enhance the pump operation for a specific setting.
• Flow Meters
• Nozzles
• Delivery Hoses
• Strainers
IMPORTANT NOTE:
The chemical resistances of any wetted materials, such as hoses and dispenser nozzles must also be considered.
See our range of available accessories that are suitable for use with our range of drum pumps.
All information provided in this article is intended as a preliminary guide only. The information contained herein does not constitute advice and some subjects briefly mentioned in this article may need further research to be fully understood. Pipe Warehouse UK is not responsible for any issues arising from the use or reliance on the information contained in this article.